EP 3115A/B is a spatial structure potting resin for high and low temperature impact requirements, in accordance with 100: 15 Weight ratio weighing and mixing, through the potting equipment supporting automatic production line, through preheating, mixing, gluing, vacuuming and heating or room temperature curing, to form a good bonding of metals and common polar plastics, and can withstand the equivalent environmental high and low temperature impact test, as well as constant temperature and humidity after the verification of physical characteristics and chemical properties. The product meets the flame retardant rating requirements of UL 94 V-0 and has considerable thermal conductivity.
All Products
Two-component High thermal conductivity Epoxy potting of electronic component
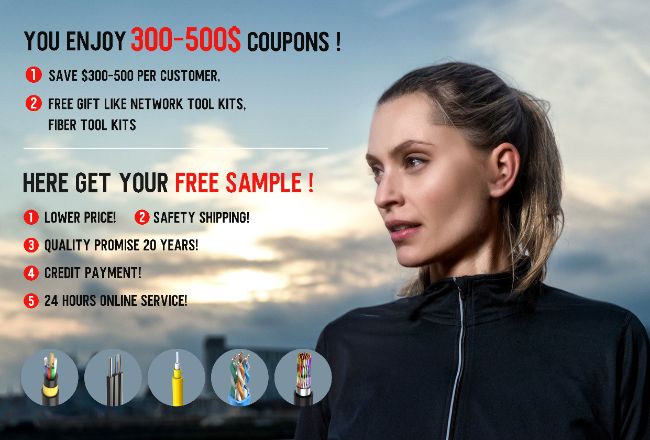
Contact me for free samples and coupons.
WhatsApp:0086 18588475571
Wechat: 0086 18588475571
Skype: sales10@aixton.com
If you have any concern, we provide 24-hour online help.
xProduct Details
Materials | Epoxy Resin | Color | Black |
---|---|---|---|
Thermal Conductivity | 0.3 | Part | Two Part |
Name | Epoxy Potting Sealant | Usage | Elelctronic Component |
Samples | Free Sample | Delivery Time | 7-10days |
Certificate | SGS, ISO ,FDA | Application | Encapsulating And Potting Of Flame Retardant |
Advantage | High Quality & Competitive Price | ODM & OEM | Yeah |
Shelf Life | 12 Months |
Product Description
We Supply Free Samples. OEM & ODM are Welcomed. we can do your logo and Brand
Two-component solventless room temperature curing epoxy potting-sealing material CompoundSpecification
Product Description
Description
Typical Applications
- Power module, high voltage DC contactor
- Permanent magnet motor stator, high voltage power supply
- Tank type reactor, high voltage capacitor
- Power tools, instruments and other packaging protection
Key Features
- Excellent adhesion and cracking resistance
- Low CTE linear expansion coefficient
- Can be cured at room temperature or by heating
- Excellent electrical insulation and stability
- Good permeability after preheating
- Suitable for space filling of various sizes
Packing Specification
*
- Code: A:2KEP6095, B:2KEP6096
- Components A and B should be protected from light, heat and sealed (can be transported and stored as non-dangerous goods); The storage period is one year.
- A Component :25kg/ plastic bucket; B Component: 3.75kg/ can.
Transport &Storage
● When stored at or below25°C in the original unopened containers, this product has a usable life of 12 months from the date of production. Sampling test is necessary for products which exceed shelf life before taking use. During storage may have little settlement stratification, stirring evenly when use, does not affect performance. It’s non-dangerous goods, can be transported as normal chemicals, CAUTION leakage during transport.
Operation process
Operation Matters
* Component A needs to be stirred evenly in the original package before use (precipitation may occur after a long time, and the performance will not be affected after the use of stirring evenly).
* Affected by temperature, there are certain differences in the curing speed of glue in different seasons, and the curing time is longer in winter. All of the above glues can be heated to accelerate curing. You can also choose to use MAXTECH winter formula.
* The A and B components of some products may crystallize and caking under low temperature conditions, which is a normal
phenomenon; Before use, put it in the oven at 80℃ to melt it, and put it to room temperature for normal use, without affecting the properties of the glue.
* During the mixing process, pay attention to the glue on the inner wall of the container and stir it back to ensure the uniformity of mixing.
Use the process
* Gluing: Stir the glue component A fully in the original package, take the A and B components according to the specified mass ratio (see the table above), mix and stir well, and then potting and sealing. The operating time after mixing is shown in the table above. After the operating time is exceeded, the glue will become sticky and no longer suitable for pouring. Therefore,the amount of glue should not be too much each time to avoid waste.
* Curing: curing conditions refer to the table above. The curing speed of glue is related to temperature, and the higher the temperature, the shorter the curing time. In winter, the temperature is low, the curing time will be extended, can be heated curing method, heating for 2 hours under the condition of 80℃. The glue can be assembled after curing and hardening. It is recommended to proceed to the next step after curing for 24 hours.
Operation Matters
* Component A needs to be stirred evenly in the original package before use (precipitation may occur after a long time, and the performance will not be affected after the use of stirring evenly).
* Affected by temperature, there are certain differences in the curing speed of glue in different seasons, and the curing time is longer in winter. All of the above glues can be heated to accelerate curing. You can also choose to use MAXTECH winter formula.
* The A and B components of some products may crystallize and caking under low temperature conditions, which is a normal
phenomenon; Before use, put it in the oven at 80℃ to melt it, and put it to room temperature for normal use, without affecting the properties of the glue.
* During the mixing process, pay attention to the glue on the inner wall of the container and stir it back to ensure the uniformity of mixing.
Use the process
* Gluing: Stir the glue component A fully in the original package, take the A and B components according to the specified mass ratio (see the table above), mix and stir well, and then potting and sealing. The operating time after mixing is shown in the table above. After the operating time is exceeded, the glue will become sticky and no longer suitable for pouring. Therefore,the amount of glue should not be too much each time to avoid waste.
* Curing: curing conditions refer to the table above. The curing speed of glue is related to temperature, and the higher the temperature, the shorter the curing time. In winter, the temperature is low, the curing time will be extended, can be heated curing method, heating for 2 hours under the condition of 80℃. The glue can be assembled after curing and hardening. It is recommended to proceed to the next step after curing for 24 hours.
Welcome to talk more with us if you have any inquiry.
Related Products
Related Products
Junction box silicone gel
One Part Silicone Sealant of electronic component
Thermal Conductivity Silicone Potting Sealant
Company Profile
Our Advantages
Certifications
Exhibition
Packing & Delivery
FAQ
Q:How long can I get a quote
A:The quotation can be provided no longer than 24hours on condition that we know all detailed requirement.
Q:Do you accept private Label?
A:Yes. ODM & OEM are Welcome.
Q:Can I get a samle before order?
A: Of course. Generally, we provide 1-3 pieces free samples for quality testing and the courier fee be born by customers. Thanks for your understanding.
Q:Do you have MOQ.
A:Yes, Generally ,MOQ is 1000pcs or 1000kg.
Q: How long will finished my order?
A: It’s depend on your order quantity.
Generally, Our production time is 10-15 days after get the payment.
Q:How to find the suitable sealant?
A: Please let me know your application purpose,substrate, application method and all your requirements. We would like give you a better recommendation.
A:The quotation can be provided no longer than 24hours on condition that we know all detailed requirement.
Q:Do you accept private Label?
A:Yes. ODM & OEM are Welcome.
Q:Can I get a samle before order?
A: Of course. Generally, we provide 1-3 pieces free samples for quality testing and the courier fee be born by customers. Thanks for your understanding.
Q:Do you have MOQ.
A:Yes, Generally ,MOQ is 1000pcs or 1000kg.
Q: How long will finished my order?
A: It’s depend on your order quantity.
Generally, Our production time is 10-15 days after get the payment.
Q:How to find the suitable sealant?
A: Please let me know your application purpose,substrate, application method and all your requirements. We would like give you a better recommendation.
As our suggestions of the sealant choose:
As a manufacturer, we would like to share with you what we have learned about the different types of potting compounds and their
characteristics. The potting compounds on the market vary in viscosity, requirements for cure conditions, among other factors.
Compounds such as polyurethane, silicone, and epoxy are widely used in a variety of applications. 1. Silicone Potting Compounds
are soft and flexible, silicone potting compounds and encapsulating materials possess a good level of elongation.Silicone potting
compound can also withstand a wide range of temperatures. Most silicone materials are able to operate at temperatures between
-40°C and 200°C. 2. Epoxy potting compounds generally perform as a better adhesive, high-temperature resistance, and chemical
resistance and have better adhesion to a wide variety of substrates and typically do not need primers. 3. Polyurethane Potting
Compounds generally have better flexibility, elongation, and abrasion resistance. 4. Acrylic Potting Compounds are UV and
heat-hardening materials, with fast hardening, adequate chemical resistance, and clear appearance.
As a manufacturer, we would like to share with you what we have learned about the different types of potting compounds and their
characteristics. The potting compounds on the market vary in viscosity, requirements for cure conditions, among other factors.
Compounds such as polyurethane, silicone, and epoxy are widely used in a variety of applications. 1. Silicone Potting Compounds
are soft and flexible, silicone potting compounds and encapsulating materials possess a good level of elongation.Silicone potting
compound can also withstand a wide range of temperatures. Most silicone materials are able to operate at temperatures between
-40°C and 200°C. 2. Epoxy potting compounds generally perform as a better adhesive, high-temperature resistance, and chemical
resistance and have better adhesion to a wide variety of substrates and typically do not need primers. 3. Polyurethane Potting
Compounds generally have better flexibility, elongation, and abrasion resistance. 4. Acrylic Potting Compounds are UV and
heat-hardening materials, with fast hardening, adequate chemical resistance, and clear appearance.
Max Tech Do the PU , Silicone, MS, Epoxy
For Automotive , Construction and Electronic Industry.We also do related tools, machines & accessories.
For More Information
Welcome to talk more with us.
Have a nice day.
For Automotive , Construction and Electronic Industry.We also do related tools, machines & accessories.
For More Information
Welcome to talk more with us.
Have a nice day.
Recommended Products